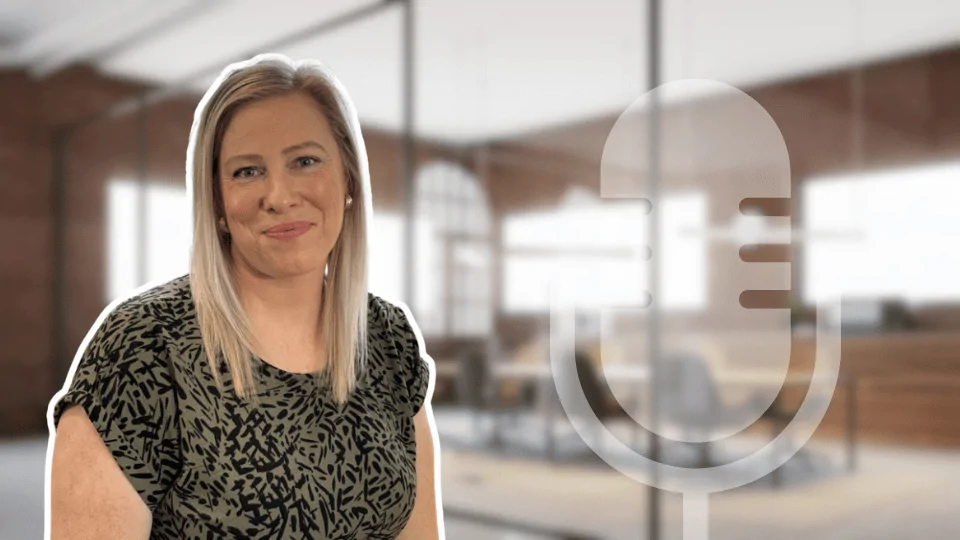
Engineering employers typically look for candidates with the right hard and soft skills. But...
Engineering employers typically look for candidates with the right hard and soft skills. But...
The Asia-Pacific region is prominent in the global renewable energy transition, driven by am...
2025 is shaping to be an exciting year for renewable energy projects in the Middle East, wit...
Engineering employers typically look for candidates with the right hard and soft skills. But...