A Brief History Of American Automotive Manufacturing
21 Oct, 20207:19October is manufacturing month in the USA, when we celebrate all those who work in this sect...
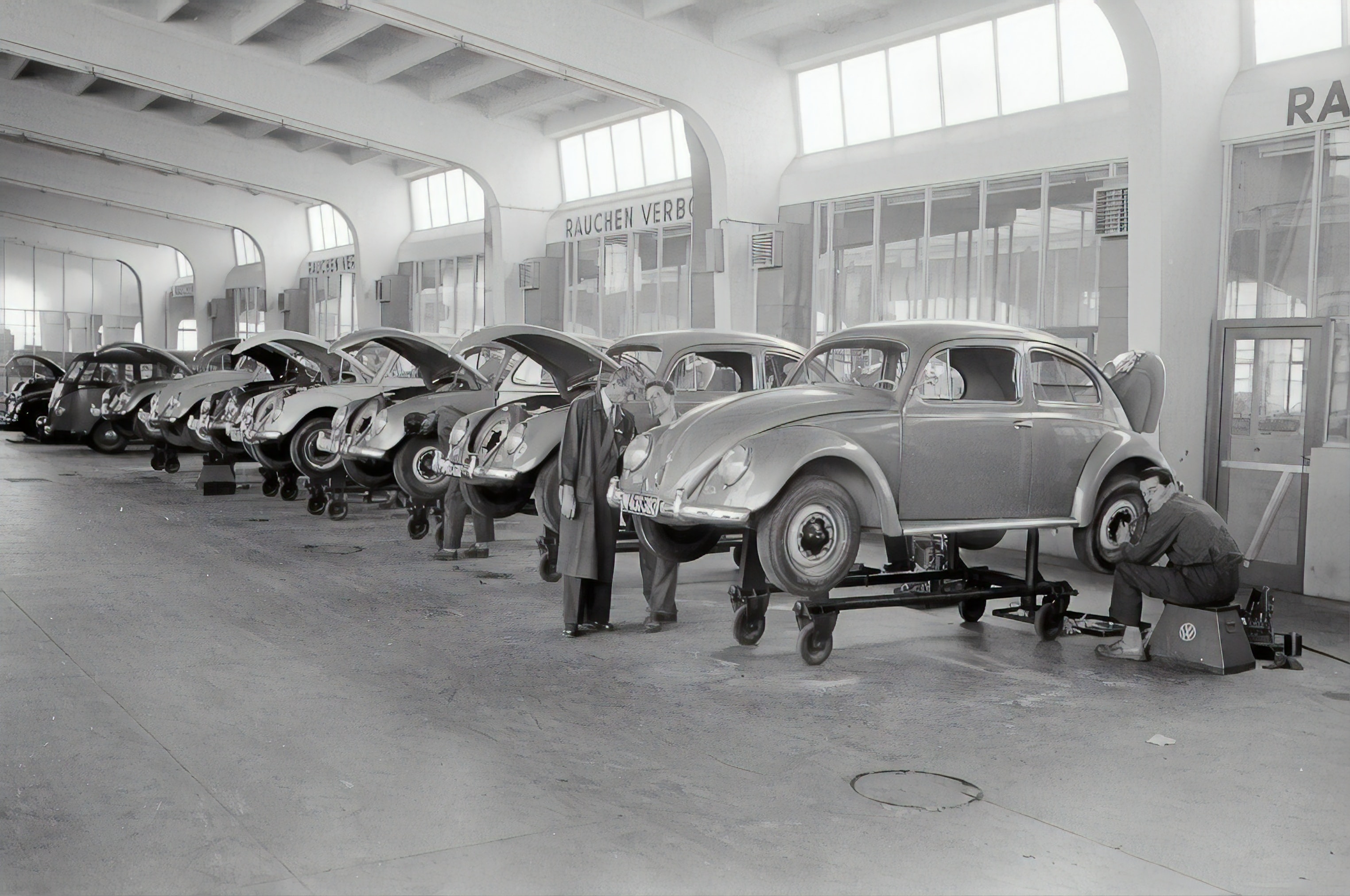
October is manufacturing month in the USA, when we celebrate all those who work in this sector, building and designing products that the rest of the world enjoy every day. Manufacturing is at the heart of American business and no industry quite encapsulates this as well as the automotive industry.
For this reason, and because NES Fircroft is a leading supplier of engineering and technical talent to America’s automotive manufacturers, we wanted to turn our attention to America’s history of automotive manufacturers and celebrate the inventive methods and designs behind some of the biggest car brands.
1850: American System of Manufacturing
America’s automotive manufacturing journey begins at a time before the first car was even invented. 1850 was the dawn of the American System of Manufacturing which would establish a reliance on efficiency and set up a greater use of machine parts.
Hand crafted manufacture is today relatively rare - reserved for “luxury” items such as Bentley cars where the slower, expert process becomes a reasoning for the higher price-point. But back in the 19th century it was the norm in British and European factories. The American system brought in standardised mechanical tools with interchangeable parts that would allow goods to be manufactured at a much faster rate with little difference between each unit. Workers no longer needed to learn complex styles or accurate designs, they just needed to learn how to operate the machine.
Manufacturing became faster, cheaper, easier and with little difference in quality from unit to unit. As the system grew in popularity across America, it would set up a vital structure responsible for the rapid growth of the automotive industry.
1864: The birth of the petrol powered car
On the other side of the Atlantic, an invention was being developed that would transform the world. German engineer Siedgried Marcus unveiled the first petrol-powered propulsive vehicle in the form of a handcart with wheels powered by an internal combustion engine. By 1885 the first automobile to go into full production would be crafted by Benz Patent-Motorwagen in Mannheim. By the end of the century they would be producing 572 units per year.
1893: The first American car
As automobile manufacture began to take off in Germany it wasn’t long before it made it over to the USA. The first successfully designed American car was created by bicycle mechanics J. Frank and Charles Duryea of Springfield, Massachusetts. Two years later the first American car race was held and won by Frank and Duryea’s vehicle. It would be on sale to the public by 1896.
By 1899 there were thirty American companies manufacturing 2,500 cars. In the following decade another 485 companies would enter the market. But only a select few would be successful enough to last.
1908: The Model T
Almost half a century after Marcus’ first design, America would get its defining vehicle: the Ford Model T.
An instant icon, the Model T was designed by the Ford Motor company in Detroit with the aim to bring “affordable” vehicles to the American middle class. Ford had developed several vehicles before this, but the Model T was the first one that the company would build all parts for itself. Following an initial success, Ford would continue to find methods to bring the price down and make it available for more people. The company famously announced that “Any customer can have a car painted any color that he wants, so long as it is black.”
Within days of release over 15,000 orders had been placed and that success would continue for years. It’s been said that at one point a “majority of Americans owned one”. But before that came a revolution in manufacturing…
1913: The first moving assembly line
Henry Ford is credited with inventing the moving assembly line, a step up from the American system of manufacturing that would allow mass production to reach new levels of speed and efficiency.
Thanks to the high volume of orders for the Model T, Ford needed to ramp up production quickly. The company opened the Highland Park plant in Michigan as a second production facility in 1910, having designed the facility expressly to suit their needs. The plant was at the time the largest manufacturing facility in the world, with around 102 acres including offices, factories and power plant and a foundry. This allowed Ford to integrate the supply chain in a way that had never been done before, setting a precedent for many modern day factories and plants.
Through continually adjusting their processes to cut costs, divide labour and keep things moving, Ford eventually came up with the moving assembly line concept, where parts are mechanically moved from workstation to workstation where they could be assembled in order without delays, issues or complexities. With 500 workstations in the Highland Park factory, Ford were able to reduce the production time of a Model T car to just under six hours.
The system was a success and brought down costs enough that Ford were able to reduce the price of the Model T to just $350. By 1927 Ford had produced more than 15 million Model Ts.
1920: The Big Three
Though the century began with plenty of competition for the American automotive industry, by the end of the 1920s the effects of the Great Depression would eliminate most of the smaller firms until the market was all but dominated by three Detroit-based companies: Ford, General Motors and Chrysler.
Throughout the middle of the century the Big Three would overcome numerous obstacles through design innovation, progressive style updates and brand strengthening. Detroit became “Motor City” and engineering professionals flocked to Michigan to work with the biggest automotive names.
1930s: Toyota’s Lean Manufacturing
Ford’s assembly line would be the biggest breakthrough in mass production but it would not remain the fastest, simplest method forever. Over in Japan, Toyota founder Sakichi Toyoda was looking to eliminate what he called the “seven wastes”: overproduction, waiting, transporting, inappropriate processing, unnecessary inventory, unnecessary/excess motion and defects. He developed the Lean Manufacturing system (sometimes known as the “Just In Time” system).
This system of working built on Ford’s assembly line but strived to cut out any process or wastage that wouldn’t create value to the end customer. This would be “The Toyota Way” for many years and would eventually become adopted by many American manufacturers in the 1980s.
1961: GM introduces industrial robots
Early industrial robots had been in existence since WWII, but wouldn’t be used in a significant way for general manufacturing for decades.
In 1961 General Motors introduced prototype robots in their Detroit facilities. These initial robots had no external sensors and no integrated circuit, so were extremely limited compared to the devices you will see in a modern facility. They were mainly used to perform spot welding, but were efficient enough that they got the attention of Ford, who wanted them in their facilities.
1960s: Introduction of CAD software
Until the 1950s computer development had reached a point where machines could help produce technical schematics such as circuit diagrams and flowcharts that could be easily modified and scaled to open up new design possibilities. In 1959 the term “Computer Aided Design (CAD) was coined.
In the mid-late ‘60s computer aided design reached the automotive industry, when Renault engineer Pierre Bézier invented the 3D CAD/CAM system that could help design parts and tools. Soon leading engineers from GM, MIT and Boeing were joining the French teams to further develop CAD tools. By the 1970’s CAD implementations had dramatically improved and were being used for various design features across all the major automotive firms.
In the following decades, CAD software would become more advanced and more indispensable, until the present day when almost every element of the design and manufacture process is monitored through some form of computer software.
1965: American Motors Corporation introduce interchangeable panels
American Motors came in to being in the mid-1950s as a competitor to the Big Three. Originally making small cars, the company came into its own in the 1960s through a manufacturing process originated by engineer Dick Teague. The concept used interchangeable body panels that would allow the company to develop multiple vehicles with different styles, all from the same stampings.
The first car to use this system was the AMC Cavalier in 1965 and was followed by the AMC AMX muscle car, the subcompact Gremlin, the Pacer, the Matador Coupe and the original Jeep Cherokee.
1980s: Technological renaissance
The ‘70s saw the rise of Japanese brands as the nation became known for smaller, more fuel efficient, well-built cars. Conversely American firms’ focus on bigger vehicles with more power clashed with new federal standards of automotive pollutants and energy consumption, plus an increase in gasoline prices following the 1973 and 79 oil shocks.
The American industry responded in the ‘80s with sleeker organisational structures and a greater reliance on technology. A five year $80 billion modernisation and retooling program was undertaken across GM, Ford and Chrysler to refresh their manufacturing processes. Detroit studios replaced styling with functional aerodynamic design and abandoned the tradition of annual cosmetic changes. CAD software and robotics were further implemented as the focus shifted towards smaller, safer, more fuel-efficient cars.
The industry continued to be a major employer across the states, accounting for one in every six jobs in 1982.
21st Century
In the 21st century, automotive design is going through a radical change with smart technology and electronic functionality taking over in importance. Tech companies have now joined with manufacturers to deliver the new generation of car and opportunities open up for a new kind of engineering professional.
But there are still many manufacturing skills that are still needed and many companies that have adapted their processes to fit. Michigan-based Grede, for example began as an iron foundry in 1920, but over the years has specialised in many forms of equipment and still produces safety-critical chassis, suspension and drivetrain components for the automotive industry, having been acquired by American Axle in 2017. Others have been around for a shorter time, but made a strong impact on the industry, such as metal sampting and components manufacturers Gestamp.
And some provide services that grow ever more important in modern vehicles. Mann+Hummel specialise in filtration, providing air filters for American vehicles - systems that now seem more vital than ever.
The future?
With a new century and new technology came new firms. The one name that has made the biggest impact in recent years is Tesla and, just as they set new standards for electric cars, they are setting new standards for manufacture.
The firm have built their first gigafactory in Storey County, Nevada, which they intend to fill with 10,000 workers. As well as setting new standards of factory size, the facility is also technologically advanced, with the intention for it to be entirely energy self-reliant, powered through a combination of on-site solar, wind and geo-thermal sources.
The company have already announced plans for additional gigafactories around the world and its safe to say that if this can be proved to be successful, sustainable and profitable they will not be the only ones working in this way.
Will the future of automotive be entirely in gigafactories? Will CAD, 3D printing and other Industry 4.0 features transform manufacturing plants to look more like ICT firms? Will the dependents on new in-vehicle technologies continue to transform what we customers look for in a car?
These are all questions that will affect the coming decades of automotive engineering. This is simply another in a long line of exciting and uncertain developments in the long and varied history of American automotive manufacturing.
Want to work in automotive manufacture?
NES Fircroft's dedicated automotive team can help you find your next job in this ever changing industry. Register your CV with us today for free to secure your next job.