What Does The Rise Of EVs Mean For The Global Automotive Workforce?
12 Jul, 2021 6:20Even just a cursory glance at the media demonstrates an ever-increasing number of stories ab...
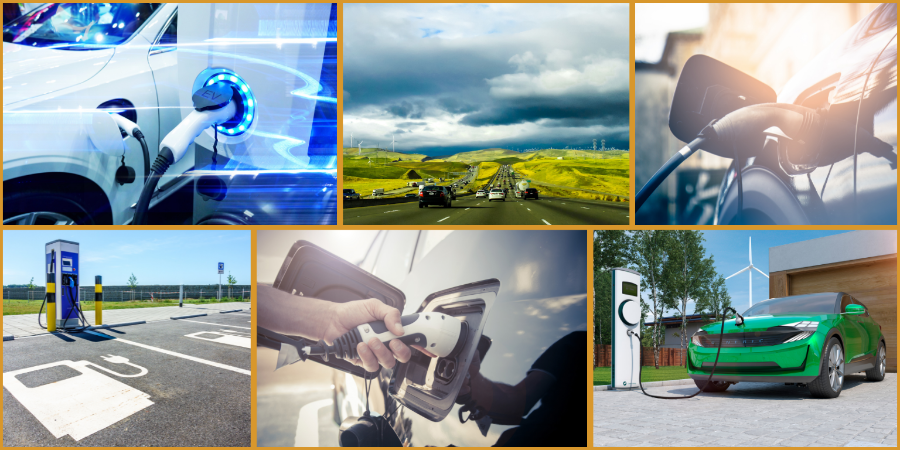
Even just a cursory glance at the media demonstrates an ever-increasing number of stories about electric vehicles (EVs), the impact they will have on energy demand, how they will lead to cleaner, greener urban environments and myriad other topics.
Yet there’s relatively little information about what EVs will mean for the automotive workforce. So, how will the rise of electric vehicles effect the manufacturing workforce?
The rise of EVs: media hype or industry reality?
In 2017, global sales of electric vehicles passed the one million mark for the first time (factoring in plug-in hybrid vehicles (PHEVs) too). In 2018, more than two million electric vehicles were sold.
By any measure, these figures demonstrate strong growth in EV sales - and point towards an ever-steeper upward curve. It’s a trend which is agreed upon by many of the major market analysis firms. Deloitte sees EV sales growing to 4 million in 2020, 12 million in 2025, before rising to 21 million in 2030. According to Deloitte’s analysis, as EV sales grow, the market penetration of ICE vehicles will decline from 2024 onwards.
Bloomberg’s New Energy Finance (BloombergNEF) research division postulates an even more optimistic take, with a recent report stating that ‘by 2040, we expect 500 million passenger EVs on the road and over 40 million commercial EVs’.
Aside from consumer demand and sales, a supportive policy and regulatory environment is also spurring the growth of EVs, taking them from the pages of the media to the reality of your local roads and highways. To date, approximately 20 cities worldwide have announced plans to phase out gasoline and diesel cars by 2030 (or in some cases sooner). Several national level bans have also been announced including the UK government making a commitment to remove petrol and diesel vehicles from public roads by 2040 (albeit hybrid vehicles will still be permitted to be sold).
With the demand for EVs growing, Automotive OEMs are responding in kind. Perhaps the starkest example of how the automotive industry is embracing EVs is the way in which they are now investing their incremental capex spend. Wells, Wires, and Wheels… a new report from BNP Paribas claims that 70% of automotive OEM’s incremental capex is now going in to EVs.
With major OEMs such as Volkswagen effectively shutting down investment in ICE technology and focusing on EVs, the overall cost differential between the two technologies will rapidly diminish. Mark Lewis, author of BNP Paribas’ Wells, Wires, and Wheels report believes that cost parity between EVs and ICE will be achieved rapidly,
“As in our previous forecasts, we expect price parity between EVs and internal combustion vehicles by the mid-2020s in most segments, though the first segment crosses by 2022.”
This has been named the ‘EV Tipping Point’.
Whichever way you look at EVs, be it from the supply or demand side, adoption and market penetration is growing, and with that comes the imperative for Automotive OEMs to change the way they configure and recruit their workforces.
The changing automotive manufacturing landscape
EVs are indeed growing, but what impact has this new technology had on the automotive industry - one which has been notoriously difficult for new entrants to break into?
What may seem like a mere change to a vehicle’s propulsion has already led to a disruption of the automotive manufacturing industry and it promises much more.
New entrants
The most notable impact of EVs upon the automotive market has been the new entrants that have arrived on the scene over the past decade. For example, Tesla very quickly gained large market share and brand recognition amongst EV-savvy consumers.
Other newcomers such as BYD, have quickly become the world’s largest manufacturer of EVs. The company may have begun life as a manufacturer of cell phone batteries, but it’s now an EV powerhouse selling 30,000 EVs per month which are developed and built by its quarter of a million employees. It’s the company leading China’s transition to clean mobility and is one of several EV brands that you're likely to become very familiar with over the coming decade.
Chinese brands such as BAIC, BYD, Chery, JAC and Hawtai could one day become automotive brand names with the same level of recognition as Ford, Chevrolet, VW and Audi.
White label OEMs
New challenger EV brands are already outcompeting incumbent OEMs, in terms of market share, consumer adoption and technological innovation. Yet, scaling up to meet the projected demand for EVs could pose major problems for new EV brands.
Forecasting production capacity and investing in new factories, tooling design, innovation and talent could prove beyond the capacity of many new market entrants, which has led several industry commentators to suggest that incumbent OEMs could become ‘white label’ suppliers to newer brands. In other words, your shiny new EV could have a Rivian badge, but have been manufactured at a Ford plant in Michigan.
Regional segmentation
Gone are the days in which a handful of brands would control the majority of the world’s automotive market.
In what has been a longer-term trend, economically developing nations such as China have developed their own domestic car industries - a trend which has been accelerated by the arrival of EVs.
The result? An automotive market which is regionally segmented like never before - creating more headaches for OEMs which seek to sell their vehicles across multiple international markets.
Markets such as China and Europe are quickly electrifying their fleets, whilst countries such as India and other emerging economies are expected to electrify much more slowly. The challenge for OEMs (and their workforces) will be the meet unbalanced demand from these markets for EVs and ICE models.
In other words. The whole world isn’t going electric all at once. OEMs will have to figure out how they respond to demand for different powertrain options from different regions.
EVs and the automotive workforce
We’ve seen how the rise of EVs will have a disruptive impact upon incumbent OEMs, challenging their existing market share, altering regional demand and even changing public perception of the industry as new brands emerge. But what impact will EVs have upon the workforce itself?
There are several clear trends which will influence how OEMs and new EV manufacturers compile, recruit and retain their workforces over the decades ahead. However, there’s one overarching trend which will apply to incumbents and start-ups alike - the need to invest in their workforce solutions.
New skill sets
The automotive industry is currently an enormous employer of technical and engineering talent across the globe. In Europe alone the automotive sector employs in the region of 3 to 3.5 million people (which adds up to 11.3 per cent of the EU’s total manufacturing employment). In the US just over 1 million people are directly employed in automotive manufacturing positions, while in China this figure stands at around 1.6 million people directly employed in automotive manufacture (as of 2017).
Do these various workforces have the necessary skills and experience to design, develop and build the EVs that are (and will be) demanded in the years ahead?
Not necessarily. The production of ICE powertrains requires a very different set of specialised skills and knowledge from those required to build an EV. At present, incumbent OEMs in particular do not have the talent on board they need to build successful EVs.
Deloitte highlights the skills dilemma facing OEMs succinctly,
“Despite the number of highly-skilled workers currently employed in the industry, the design and manufacture of EVs will require a substantial investment in new talent. Working with battery packs instead of ICEs requires OEMs to increase both the breadth and depth of knowledge within their pool of engineers. The shift to EVs means that multi-skilled engineers, who are as comfortable with chemistry as they are with electrical and mechanical engineering, are required. This is a challenge as multi-skilled engineers are scarce and as such, they generally demand higher wages.”
The key takeaway for Hiring Managers should be the need to foster multi-disciplinary teams especially those that pivot around mechatronics. Mechatronics is a combination of electrical and mechanical engineering and is used for designing and managing (and linking) different steps of the production process e.g. equipping cars with electronic actuators, wired and wireless communication within the car, information storage and strategic control systems.
Other areas of focus should include the sourcing of experts in IT and consumer electronics (especially if EVs also combine a level of autonomy). A study conducted by researchers Elmer-Dewitt in 2015 concluded that
‘knowledge transfer from smartphone technology components and systems will be an asset in manufacturing future electric vehicles’.
OEMs will need to change the composition of their workforces. Engineers with a broader range of skills, and specialist knowledge in battery packs, chemistry and advanced electronics should be the targets of Hiring Managers looking to secure an ‘EV ready workforce’.
The lure of the start-up
As OEMs seek to staff up in preparation of EV design, development, and construction, they will face a stiff level of competition from a wealth of new start-ups. As Deloitte put it
“Building the workforce of the future becomes even more challenging for OEMs when the best and the brightest science, technology, engineering and mathematics (STEM) graduates are increasingly drawn to start-ups."
Thus, a well-crafted, considered Employer Value Proposition (EVP) will be vital for OEMs that want to secure the best new talent for their EV projects. Competing against vibrant start-ups that offer modern working spaces, remote working, unlimited holidays and other such perks means that incumbent OEMs will have to think very differently about recruiting and retaining staff.
An electrical revolution
Already the automotive industry looks very different than it did 10 or even 5 years ago, and that’s thanks to EVs. EVs are disrupting the global automotive industry, introducing new brands, new technologies, new business models and new people.
Secure the automotive workforce of the future with NES Fircroft
NES Fircroft provides skilled personnel for Automotive jobs on a permanent and contract basis. Having operated in this sector for a number of years we have strong relationships with some of the biggest companies in the industry. If you're looking for a new role, browse our job vacancies.
For over 20 years, we’ve sourced and managed personnel for the automotive industry, within OEM, Tier 1 & 2, Motorsports and Commercial, across disciplines such as design, engineering and manufacturing. If you have a staffing requirement, get in touch with our experts.