Everything You Need To Know About Offshore Decommissioning
03 Jul, 20198:24As Oil & Gas fields reach the end of their lifespan, they must be decommissioned. This c...
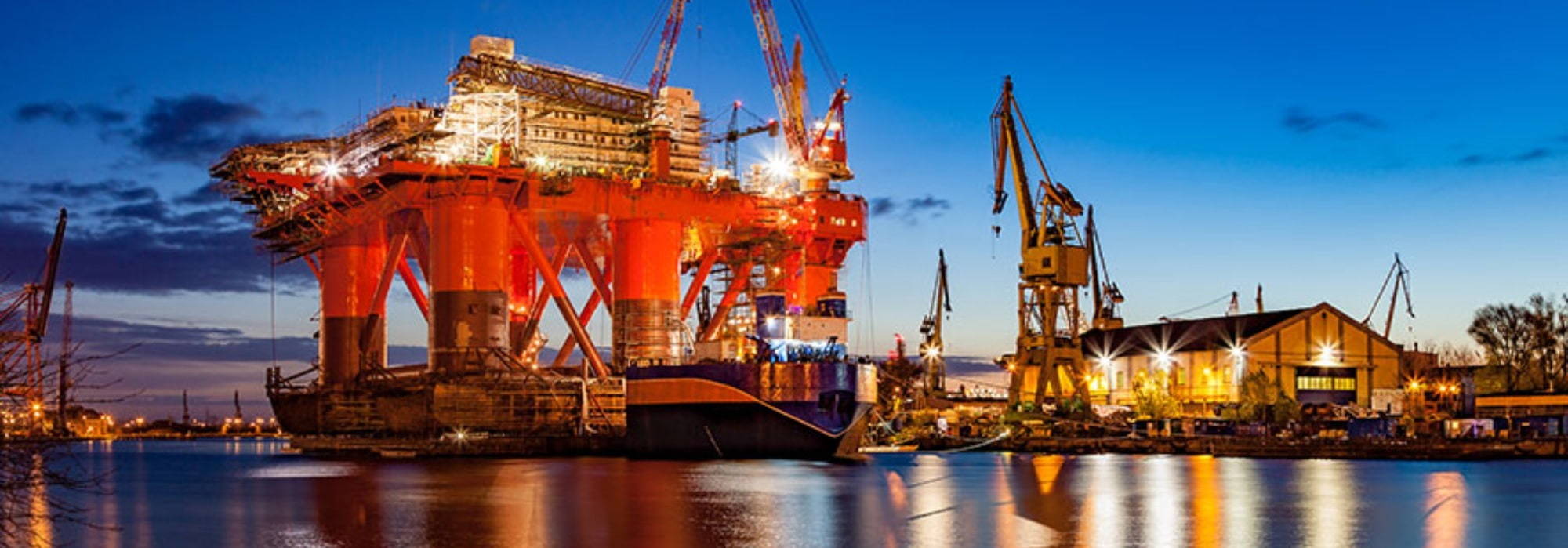
As Oil & Gas fields reach the end of their lifespan, they must be decommissioned. This complex task involves a number of highly skilled workers to ensure that the wells and platforms are safely and efficiently dismantled and removed. With a huge number of offshore rigs expected to reach the end of their production cycle over the next ten years, the global need for technical decommissioning specialists is expected to grow, with annual spending projected to reach $13 billion within the next 25 years.
To prepare you for the rapid expansion of this part of the industry, here's everything you need to know about offshore decommissioning.
What is decommissioning?
Decommissioning is the term used to describe the final stage of an energy project. In oil and gas, when a field production cycle comes to an end and all the usable fuel has been processed, the facilities must be dismantled and the surrounding area returned to its natural condition. This is a legal condition as set out by the Petroleum Act 1998.
The process involves clearing and filling the well, and removing the infrastructure and platform. In some cases certain parts of the conductor pipes can be left in place to form artificial reefs for ocean life, but most are fully cleared to ensure minimal environmental impact.
Platform elements can be reused or recycled for other projects, or can be disposed of for scrap once back onshore. Once removed, the ocean floor is cleared of all debris in order to ensure it is returned to its pre-lease condition.
Due to the amount of offshore Oil & Gas fields that have been developed over the last few decades, there is a growing number of platforms reaching the end of their lifespans. Abandonment and decommissioning is a fast-expanding industry that is expected to turn over billions in revenue, and create thousands of jobs globally.
What does decommissioning an offshore oil platform entail?
Decommissioning is a long and complex process. It’s a massive engineering task that requires almost as many workers as it takes to man a fully operating platform. The platform must be cleared of all equipment, the well plugged and all elements of the infrastructure removed from the seabed.
There are ten stages in total when decommissioning an offshore oil rig:
1. Project management
The initial preparation begins up to three years before the well runs dry. Contractual obligations must be reviewed to ensure decommission and lease follows the procedure agreed years before at the beginning of the well’s lifespan. The size of the decommissioning task means resources and financing must be organised far in advance in the same way as construction of a new well project would need to be managed. Specialist contractors must be sought for each technical aspect of the project.
2. Engineering and planning
Engineering analyses must be run across the entire project in order to create a comprehensive plan for the decommissioning work. Safety and environmental factors must be taken into account for the breakdown and removal of each part of the platform. Each separate operation making up the following stages of decommissioning must be planned out well in advance.
3. Permitting and regulatory compliance
Like any new construction or oil & gas project, there are numerous legal and regulatory factors which must be resolved before any work can be undertaken. Obtaining the right permits for a project of this size can take years to complete. Depending on the location of the well, local laws must be adhered to - North Sea rigs for example are subject to the Petroleum Act 1998 and the OSPAR convention agreed to by representatives of 15 countries in 1992. Environmental factors and the effects of the planned work play a large part in having the permits approved, and operators must ensure they have a comprehensive plan and provide up-to-date surveys of the area surrounding the project.
4. Oil platform preparation
Before the full decommissioning process can be undertaken, the oil platform must be prepared. A primary aspect of this is purging it of residual hydrocarbons - essentially cleaning out all the pipes, tanks, equipment and any other areas that might contain hazardous materials or residue from drilling. It’s important to ensure that the least possible amount is released back into the sea when the process is underway.
In addition, platform equipment and anything not part of the infrastructure is removed at this point. Piping and cables are cut between deck modules. Padeyes are installed to lift the modules. The structure is reinforced. Underwater workers remove marine growth and prepare the jacket facilities for removal.
5. Well plugging and abandonment
This is the main element of the decommissioning process and is the largest cost of the project. The wellbore must be cleaned out and plugs carefully installed in the well. It’s important that this is done correctly in order to prevent any environmental issues from leaving the underwater well open. Once the well has been emptied of downhole equipment, cleaned out and filled with fluid; the open hole and any perforated intervals at the bottom of the well can be plugged. Casing stubs, annular space and a surface plug are also fitted, with fluid filling out the spacing between plugs.
The plugs are pressure tested before the process begins to ensure integrity, and tagged to ensure proper placement. There is a significant amount of planning and inspection work involved at this point, as any errors could cause significant problems.
Once the well is plugged it is considered abandoned as no more production is possible. All that remains is to take apart and clear up the infrastructure.
6. Conductor removal
The conductor pipe provides the initial stable structural foundation for an oil well. The pipe and its casings must be removed to at least 15ft below the ocean floor, unless a regional supervisor approves otherwise (based on the type of structure or ocean-bottom conditions).
Removing these is a lengthy process that involves severing the casings in to 40ft sections using explosive, mechanical or abrasive cutting. The segments are then pulled apart with casing jacks, and offloaded using a rental crane on a platform staging area. The sections can then be offloaded on to a boat to be taken back to port for transportation to an onshore disposal site.
Cutting the sections provides the most complicated issue, with several methods available - each with its own benefits and drawbacks.
Explosives can be lowered in to the piles from the surface to the optimal place to sever the casings. Detonating is the fastest method of severing, and is also the lowest costing option. However there are obvious safety concerns and environmental issues.
Abrasives create a clean cut by injecting sand or slurry in to a high pressure water jet that wears away at the steel. This can cut through with very little shock to the structure, but requires a large deck space to contain the materials. Not every platform is suitable.
ID Cutters are a mechanical tool that can be lowered in to the interior pipe and activated to cut from the inside out. These are the easiest way to cut the sections buried below the mudline, but can be difficult to manage due to poor visibility within the pipe, and can be hindered by obstructions.
Diamond Wire Saws can cut straight through the steel, concrete and aggregate of that make up the conductor pipe and casings, and can be easily controlled for effective cutting of larger wall sections. They’re also more environmentally friendly than other methods. However they take up a lot of space, so are only usable if there’s enough clearance on the outside of the structure. Plus they can’t cut below the mudline, so the area must be dredged first, which requires further equipment and work.
Operators must find the most effective, practical method for cutting at the planning stage, depending on the conditions of the area, type of structure and needs of the project.
7. Mobilisation and demobilisation of derrick barges
Derrick barges are required to lift and transport the platform. During the planning stage it will be established how the topside is going to be removed - either in one piece, in groups of modules or in smaller pieces. The method will determine the size and lifting capacity of the derrick barge. The project manager will also have to take in to account the crane capacity at the offloading site.
8. Oil platform removal
Smaller platforms are often removed in one go on to a derrick barge with enough lifting capacity. Removing combined modules at once is similarly beneficial - requiring fewer lifts and saving time and money, but requires the modules to be positioned in an optimal way.
The most common method is to dismantle the topsides in the reverse order from which they were installed or, if necessary, cut them in to smaller pieces which can be removed with platform cranes or temporary deck mounted cranes. This can save some costs through use of a smaller derrick barge, but takes much longer.
Following the topside removal, the jacket and subsea elements can be removed. Similar to the conductor removal, the jacket must be cut in to sections by divers using explosives, mechanical cutters, torches or abrasives. If they’re in less than 200ft of water they can be removed in a single lift, otherwise they need to be taken in smaller pieces. Everything must be removed down to 15ft below the mudline.
9. Pipeline and power cable decommissioning
If pipelines or power cables are considered by the BOEMRE not to pose an environmental hazard, or will not interfere with navigation or commercial fishing operations, they can be decommissioned and left where they are. For pipelines, this involves flushing it with water, disconnecting it from the platform and then filling with seawater. The open end is then plugged and buried under concrete, 3ft below the seafloor.
If the BOEMRE rules that it is a hazard during their review at the permit stage, all elements must be removed along with the rest of the platform elements.
10. Materials Disposal and Site Clearance
Depending on the condition and type of the platform, elements can be reused or refurbished for other projects. Otherwise it can either be transported to other areas of the sea where it can form artificial reefs, or scrapped in specialised landfills or fabrication yards.
The site must then be cleared, beginning with surveys to map out any debris left from the removal process and note any environmental damage. Remotely operated underwater vehicles (ROV) or divers are deployed to remove any debris and scan the area further. Finally, test trawling is undertaken to verify that the area is clear.
What types of jobs are involved with offshore decommissioning?
Such a lengthy and complex process obviously requires a huge number of skilled, technical workers for each stage. A decommissioning project provides jobs for:
Civil engineers
Maritime engineers
Safety engineers
Project managers
Surveyors
Waste management consultants.
The size of the global Oil & Gas decommissioning market
As the wells that led the offshore Oil & Gas boom reach the end of their lifespan, decommissioning is becoming a progressively bigger industry. In the North Sea alone, there are roughly 170 oil installations, 10,000km of pipeline and 5,000 wells. Each one of these will eventually reach the end of their production cycle and require decommissioning.
The Offshore Decommissioning Study Report commissioned by the IHS Market states that in 2015, spending on decommissioning projects was approximately $2.4 billion - but by 2040 will reach $13 billion per year. That’s an increase of 540% in just 25 years.
Within that timeframe we’re due to see massive changes in the industry. Between 2016 and 2021 it’s estimated that around 600 offshore assets will be decommissioned globally. With the majority of projects taking place in the North Sea, Europe is expected to absorb approximately 50% of global spending by 2021.
To take a look just at the North Sea, it’s expected that within the next 7 years, the decommissioning industry on the UK Continental Shelf will be worth around £17.6 billion. Over the next decade over 100 platforms are forecast for removal, over 1,800 wells will be plugged and almost 7,500km of pipeline will be decommissioned.
At peak times, this will provide somewhere between 16,925 - 22,775 jobs in Scotland alone.
What does the future of Offshore decommissioning look like?
Oil & Gas wells are not the only offshore platforms that will need decommissioning as we look further to the future. In 2015 the Yttre Stengrund in Sweden became the first wind farm to be decommissioned, after 27 years of operation.
With the average lifespan of a wind turbine at 20-25 years, the future of offshore decommissioning is clearly not limited to the Oil & Gas industry. Even well maintained farms can not last forever, and environmental effects such as lightning strikes and erosion ensure that there will always be a time when the turbines need dismantling.
A report by Arup estimates that the cost of decommissioning all the currently operational wind farms off the coast of the UK will reach £3.6 billion. And with more turbines being built all the time, the opportunities for future decommissioning roles will continue to grow.
Decommissioning: a growing source of Oil & Gas and Renewables jobs
If you have the expertise to join the biggest names in offshore decommissioning, NES Fircroft can help. Our half-century of experience in recruiting top talent for all aspects of the energy spectrum means that we’re experts in finding the right people for the right technical roles. To keep up to date with the latest job opportunities, register with us.
If you're new to the oil and gas industry and need help familiarising yourself with some of the industry's jargon, check out our oil and gas terminology series.